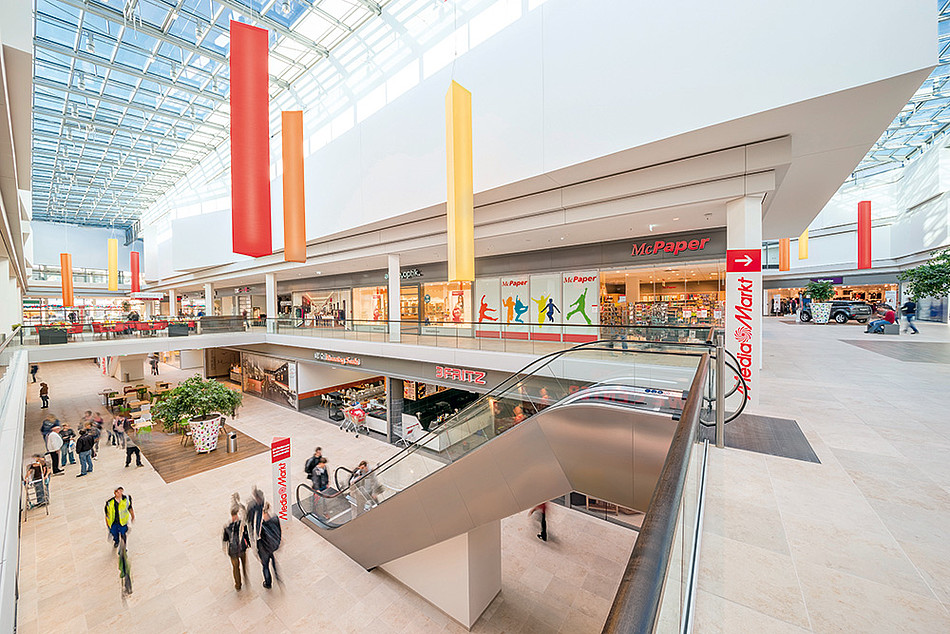
Shopping, living and enjoyment – that is what the "NeuerMarkt" shopping mall is all about. The name has not come about by chance; after all, the mall’s 14,000 square meters of rental space is located on the edge of the historic old town of Neumarkt in the Upper Palatinate, Germany. You have pretty much all you could wish for here: shops from all conceivable sectors, a wide range of restaurants, a large movie theater, a fitness studio, a 4-star hotel and an underground car park. The builder and operator is the international Max Bögl group, which has its headquarters in nearby Sengenthal. The company had attention to innovation and quality at the front of their minds when selecting the facilities. For example, the building services system needed to be particularly energy-efficient to meet tenants’ individual requirements. Max Bögl commissioned Kieback&Peter to achieve this by integrating heating, ventilation, air conditioning and fire protection for the €100 million new building into a smart automation solution – a large task to be completed in a very tight timeframe.
A Birthday Deadline
The client’s birthday on September 17, 2015 set a very tight deadline for the team of experts at the Nuremberg branch to plan and integrate their work: this day had been set as the official opening of the NeuerMarkt mall. All the work had to be completed and the systems fully functioning by then. Alfred Schwemmer, Deputy Branch Manager, reflected on how extensive and demanding the objectives were, and in such a short time. The task was to deliver the building automation as a complete solution including all cabling, integration of sensors and actuators as well as constructing a switch cabinet. In addition to implementing tenant-specific supply to around 40 shops, restaurants and commercial areas, a sophisticated ventilation system for the movie theater was also required. Integrating 270 calibration-compliant cool/heat, electricity and water meters also proved particularly challenging. These measured values had to be digitally bundled via the automation solution and then sorted by consumer to be transmitted to administration for billing.
All Operating States on a Flat Screen Monitor
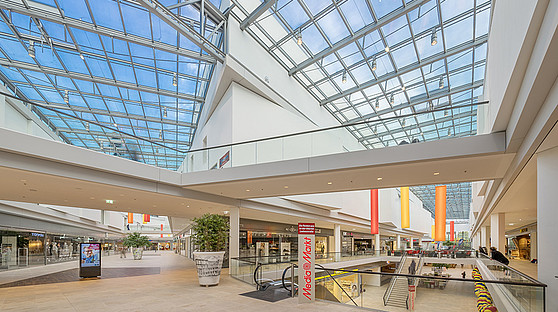
Kieback&Peter’s Nuremberg team pulled all its available capacities together and used concentrated manpower to complete the tasks in a very short time. They kept in close contact with the client and future tenants. The result: they were able to hand over the required system to the client on time and in fulfilment with all requirements. The experts set up eight technical centers with 10 control cabinets (information centers, IC) in the building, integrated two chillers and created a smart automation centerpiece using Neutrino BMS central monitoring and control software. The building management system (BMS) works on a high-performance BMS computer in the facility manager’s office, clearly visualizing all the system components and operating states on a flat screen. The BMS communicates with the ICs via cabling/IP. This is where the actual physical switching operations take place. They are carried out by 16 smart and flexible Kieback&Peter DDC4200 controllers. They communicate with the Neutrino BMS, with each other as well as with field devices located at approximately 4,100 physical data points throughout the building.
Field Devices as Workers Covering a Wide Field
The team has integrated numerous field devices into the "NeuerMarkt" mall; these ensure, for example, that all technical building systems work perfectly at all times, automatically providing pleasant temperatures and fresh air: MD200Y electric actuators control the heating control valves and SM24 damper actuators control the ventilation functions. They carry out the DDC's control commands, issued on the basis of measured values from numerous sensors as well as the specified setpoints.
Kieback&Peter had to take different needs into account depending on the respective rental unit’s business needs—for example, a restaurant unit with a kitchen needs different ventilation solutions than a drugstore. Here, too, Alfred Schwemmer and the team found solutions tailored to these needs: each rental unit received a tenant transfer box with FBM fieldbus modules with corresponding I/O interfaces for individual requirements.
A Great Movie Theater, Especially from a Technical Point of View
The most unusual task for the team was the ventilation control in the seven movie theaters. Their energy-saving automation solution takes into account both the actual number of guests per theater as well as the temperature and CO2 content of the air, measured via transducers, which are also ‘Made by Kieback&Peter’. The theater operators were provided with two touch panels featuring intuitive user guidance, enabling them to learn to operate their system themselves quickly and easily.
The 270 consumption meters from third-party suppliers that had to be integrated proved a tough nut to crack: the experts integrated them into the smart system via the M-Bus protocol. The measured values of each meter are continuously recorded by the building automation system, stored centrally and can be transmitted via data export to the center administration’s accounting system. “The large number of meters makes it very time-consuming to truly ensure that all meter values were transmitted and assigned according to their calibration,” remembers Alfred Schwemmer. At the combined opening and birthday celebrations of the client and "NeuerMarkt" mall, he and the team of experts toasted the successful automation project.