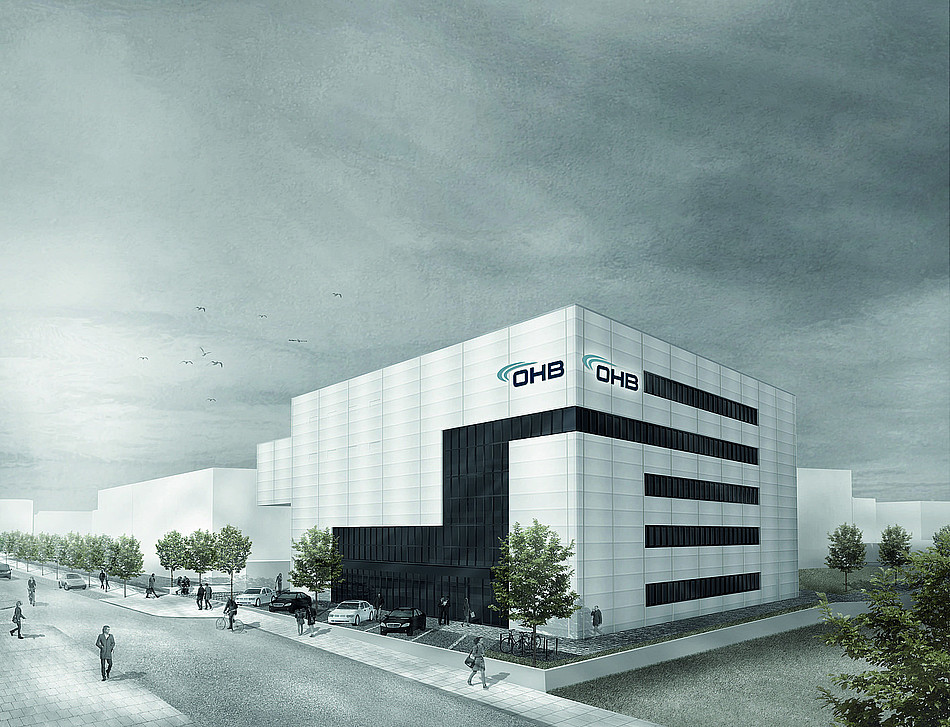
The manufacture of satellites and systems for highly complex space missions requires absolutely precise environmental conditions. This likewise applies to the new PLATO hall of the space and technology group OHB SE, commissioned by the listed family company on Lise-Meitner-Straße in Bremen in the fall of 2018. Among other equipment, satellite platforms and components for various European Space Agency (ESA) satellite missions are manufactured here in an area of around 1,000 square meters, under cleanroom conditions. The company invested 14 million euros in the building, which also includes a five-story office complex with about 1,500 square meters of floor space. The ventilation system control technology for the eleven-meter-high cleanrooms was designed with especially stringent parameters — the air quality must be precisely maintained at all times. Owing to prior work successfully completed for OHB SE, Kieback&Peter's Bremen branch was commissioned to integrate the control of ventilation, heating and air conditioning into a digital automation solution.
Highest requirements for clean air
"Overpressure control of ventilation systems for class ISO 8 cleanrooms" stated the order from OHB as project manager Torben Luer from Kieback&Peter reviewed the required tasks. This detail of the PLATO hall project posed the biggest challenge for the team of experienced technicians and engineers. This is because the ISO 8 purity class stipulates a maximum of 30,000 particles larger than five micrometers existing in one cubic meter of air. One micrometer corresponds to one millionth of a meter; for context: a human hair is 50 micrometers thick. In addition, the specifications required fail-safe components throughout the control system. Systems from other suppliers were also to be integrated into the desired automation solution. Each stipulation on its own was no easy feat – but rather than space engineering, it simply comprised the bread and butter of the Kieback&Peter team.
Time pressure and overpressure
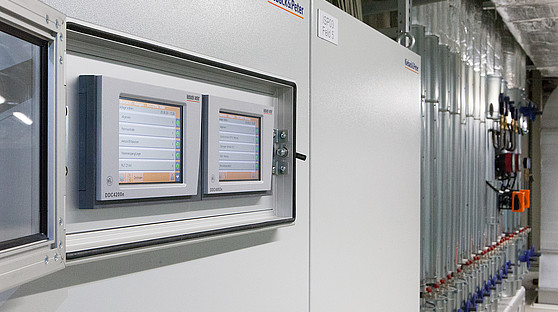
Once the order was submitted in the fall of 2019, the project needed to get underway quickly, as the PLATO hall and the office building were to be completed as early as spring 2020 – this called for strict adherence to a tight schedule. The team developed an automation solution for the cleanrooms, ensuring overpressure operation via the ventilation system in three zones, separated from each other by rolling doors. Starting from the cleanrooms, the air pressure gradually drops across the warehouse and delivery zone. This ensures that no unfiltered air from outside can enter the highly sensitive area where parts for satellites and space stations are produced. Two important components of Kieback&Peter’s smart solution are differential pressure sensors and variable volume flow controllers (actuators), which continuously maintain the required conditions, even under changing environmental influences. The air volume required in each case is supplied constantly, specific to the cleanroom areas.
Redundancy ensures operational reliability
At the heart of the building automation are the flexible and powerful DDC4000 series controllers, produced in Germany by Kieback&Peter. The controllers have four informational focal points pertaining to the PLATO hall and the office building – these are control cabinets that are connected to all of the field devices (sensors and actuators) at around 1,200 physical data points. Here, the DDC controllers carry out switching operations based on the target specifications and the measured values received. The automation system leverages a redundant design for maximum failure safety and operational reliability – if a system component fails, its respective "twin" immediately steps in and takes over. The automation is centrally controlled and monitored via Kieback&Peter’s Neutrino-GLT building management system. This software solution was already in use at OHB SE for existing buildings, so the additional systems were seamlessly integrated into the existing management system. The Neutrino-GLT works virtually through the group's computer center and clearly visualizes all operating states, along with target and actual values of the integrated system components. If, for example, the supply air’s target temperature needs to be changed in a certain room, this can be done at a PC workstation with just a few clicks using the Neutrino-GLT. In the event of malfunction, the company's on-duty service technician immediately receives an e-mail notification.
A smart solution for every challenge
In addition to ventilation units, other integrated parts included variable air volume controllers and fire dampers (integrated into the automation solution via the world-standard BACnet/IP protocol), and refrigeration systems and dry coolers sourced from third-party suppliers. These appliances communicate through Modbus, which didn’t pose a problem, as the flexible DDC controllers from Kieback&Peter also reliably process other protocols such as Modbus via gateway. The Kieback&Peter team from Bremen turned every challenge into smart, customized solution for the PLATO hall project. Result: Clean work begets clean air – after only a few months of integration work, the commissioned building automation system was running perfectly and was ready to start working under load just in time for the opening.