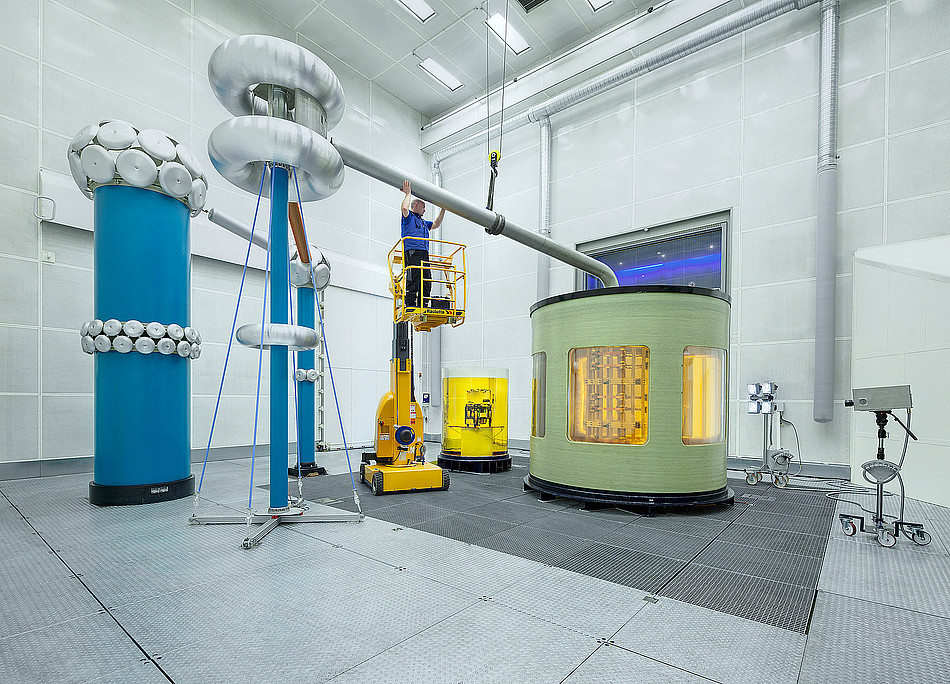
Pioneering high-voltage technology is the core business of Maschinenfabrik Reinhausen (MR). This global company, with around 3,400 employees and a strong tradition spanning over 150 years, also develops and manufactures solutions for the production of renewable energies – a key contribution to combating climate change. So it wasn’t any surprise that MR wanted to make the production and administration buildings at its headquarters in Regensburg as energy-efficient as possible. Naturally, the high-tech experts wanted a high-tech solution to their requirements, and therefore commissioned Kieback&Peter with a challenging project: They asked the automation specialists to optimize all existing heating and ventilation control systems using artificial intelligence (AI) so as to considerably – and above all measurably – lower energy consumption for the buildings while maintaining the same level of comfort. Essentially, to try to fit a square peg into a round hole – but Kieback&Peter already had the ideal solution up its sleeve.
A high-tech solution for a high-tech manufacturer
![[Translate to English:] Luftaufnahme Maschinenfabrik Reinhausen](/fileadmin/_processed_/e/c/csm_MR_Standort_Reinhausen_480b0fd354.jpg)
At its two locations in Regensburg, Germany, Maschinenfabrik Reinhausen develops and manufactures complex components for transmitting electrical energy in the high-voltage range – for example on-load tap-changers, voltage regulators and voltage converters. In 2020, the company decided to optimize the building services in its administrative and production buildings at the Reinhausen and Haslbach sites in Regensburg in order to achieve maximum energy and cost efficiency. This was to be done by implementing fundamentally new control variables for heating, ventilation and air conditioning. These variables would also help shrink the company’s carbon footprint in order to counteract climate change. Since Kieback&Peter had already worked with MR for many years and had implemented their existing building automation systems, the high-voltage experts commissioned the team from the Regensburg branch to find the perfect solution for their ambitious energy-saving goal. “It was a really exciting challenge,” sums up sales engineer Wolfgang Tux from Kieback&Peter’s Regensburg branch. He was responsible for ensuring that customer requirements were met in full and on schedule.
As much as necessary, as little as possible – thanks to artificial intelligence (AI)
The biggest challenge for the experienced automation experts was to optimize the plant controls – which were already working well – so as to achieve substantial and measurable savings without sacrificing comfort. To do this, the team opted to use en:predict from Kieback&Peter – a self-learning algorithm which controls heating and ventilation proactively and precisely in line with demand at all times. In keeping with the motto: as much as necessary, as little as possible.
Like second sight, only more accurate and smarter
How exactly does artificial intelligence help save energy? Wolfgang Tux explains: “We modified the en:predict algorithm specifically for the MR project and integrated it into the existing building automation system. To start with, the AI progressively learned the building behavior by recording and processing all operating states with the respective influences – both internal, such as employee occupancy and thermal loads, and external, such as the weather and season. From this, en:predict developed a digital image of the building, a so-called “digital twin”. For example, en:predict “familiarized itself” with the heating behavior of the building taking the weather conditions into account and, after a period of learning, was able to reliably predict how high the upcoming energy requirement would be and thus activate the systems for predictive control. After a period of exclusive “learning”, Wolfgang Tux and his team decided that the smart algorithm had acquired all the important information and activated en:predict as the central control variable for building automation.
en:predict detects how high the heating demand will be
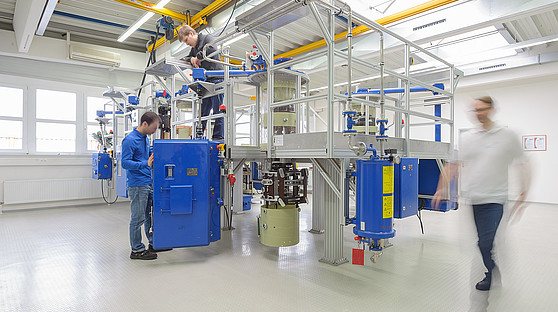
The initial test runs of the new predictive control system were already extremely successful: Since en:predict was actually able to accurately predict the behavior of the buildings, there was little need for rework: “The only significant teething problems were air flow monitors that tried to intervene in ways that contradicted en:predict. We were able to quickly eliminate this problem by fine-tuning the programming.” en:predict has been controlling the heating, air conditioning and ventilation of several halls at the Regensburg site of Maschinenfabrik Reinhausen since August 2021– with the desired effect. For example, based on the values “Monday morning,” “night temperature,” “season” and “weather forecast,” the system can calculate in advance the output that ventilation systems must provide in order to achieve the desired comfort in the different areas of the building.
Savings with en:predict per year at Maschinenfabrik Reinhausen
Energy consumption saved through en:predict
CO₂ emissions reduced by en:predict
Total savings through en:predict
Measurable savings of 43 percent – clearly visualized on the dashboard
An important part of the brief was that the reduction in energy consumption achieved by the new self-learning control system should be significant, measurable and therefore verifiable. Wolfgang Tux and his team had a solution for this as well: “We integrated a virtual dashboard in the central building management system, which allows Maschinenfabrik Reinhausen to view all energy consumption and savings clearly and logically at any time.” The dashboard offers numerous evaluation and visualization options. Above all, it shows that the project succeeded in its key objective: With the help of en:predict Maschinenfabrik Reinhausen is now able to save up to 43 percent of its primary energy and significantly reduce its carbon footprint, while maintaining the same level of comfort.