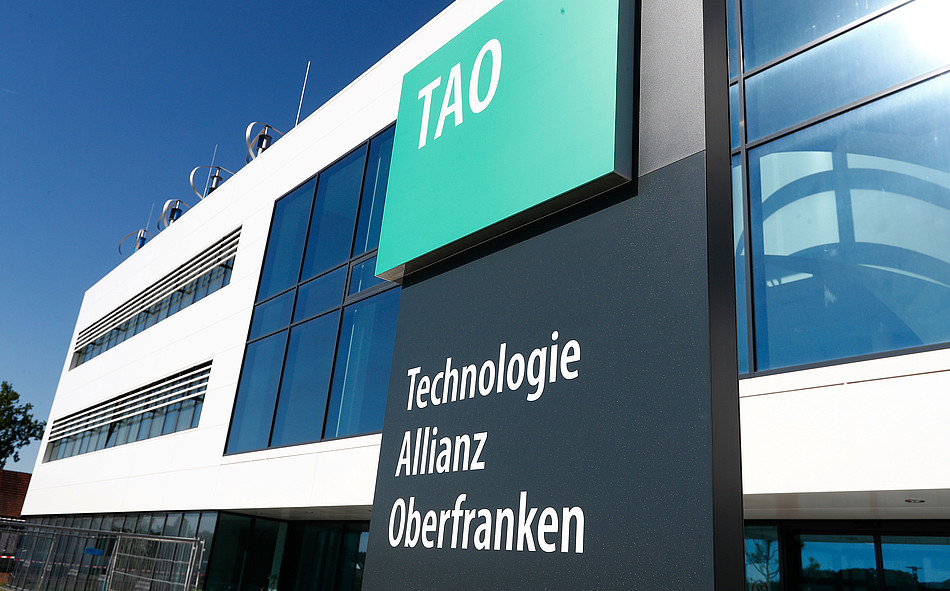
The University of Bayreuth aspires to offer excellence both in teaching and its equipment. The Free State of Bavaria has therefore strengthened the field of natural sciences. As part of the “Technology Alliance of Upper Franconia (TAO),” the new centers for “Materials Science and Technology” and “Energy Technology” were established on the Bayreuth Campus. Between 2016 and 2018, the TAO building, a 5,560 square metre high-tech new building, was constructed for three university chairs. 4,000 square meters of these are taken up by laboratories and workshops containing highly sensitive precision equipment such as electron microscopes. The State Building Authority commissioned Kieback&Peter to plan and integrate the complete building automation system. No easy task—as the scientists required an extraordinarily complex heating, air-conditioning and ventilation system whose heat pump/ice-storage technology could also be used for research by users.
Building automation, smartly controlled for science
Innovative energy use is not only part of scientific research in the new university building. The clients of the TAO building wanted an innovative heating and air-conditioning system that the university itself could also use for research purposes. On the one hand, the combination of heat pumps and a 500 cubic metre ice storage system should be able to supply heating energy and cooling for the entire new building. On the other hand, a gas-fired combined heat and power plant, a gas condensing boiler and refrigeration machines should be able to supply the useful areas with a simple control command. "The building has become like a complex automaton in which one can both study and do research," says Alfred Schwemmer about the university building. He is head of the Kieback&Peter branch in Nuremberg.
A special challenge for Schwemmer’s team of experts was planning the control matrix that had been commissioned for the various energy sources, as they had to program an individual closed-loop control algorithm. Alfred Schwemmer sums up: “The flexible choice of energy source was a particular challenge. Our closed-loop control has to adapt the different outputs of the various systems to the precise respective requirements. The specified values for temperature or humidity must prevail around the clock in the laboratories. That was exciting.” For the rooms of the electron microscopes, particularly precise atmospheric target values were also prescribed.
It was a particular challenge to make the systems controlled by Kieback&Peter accessible to researchers at the university for studies. The Kieback&Peter team had to make sure the scientists could have continuous access to a large number of operational data and processes. And there was another crucial point: the existing buildings of the Bayreuth-based Alma Mater use a third-party building management system, so the solution commissioned by Kieback&Peter had to be integrated into this existing system.
A control system whose data even interests researchers
“Everything is possible with expertise,” Alfred Schwemmer sums up his team’s recipe for success. They managed to meet all of the client’s requirements on time. The result is a smart yet highly complex building automation system. At the heart of this are 19 flexible and powerful DDC4000 controllers from Kieback&Peter. They work in 15 switch cabinets distributed over the whole of the new TAO building. The DDCs communicate not only with each other, but also with the field devices at 5,000 physical data points as well as with the third-party supplier’s central building management system via BACnet. The actual physical switching operations take place in these control cabinets, the information centers: As sensors, some field devices provide actual values such as temperature or flow rate. The other field devices, the actuators, execute the DDCs’ control commands. For example, “Reduce flow rate to 37%” or “Open damper to 82%.” For example, the Nuremberg team of experts installed 175 TD12 room temperature sensors, enabling the DDCs limit value monitoring functions. As actuators, they have installed, among others, the MD200Y actuators, also a durable hardware product from Kieback&Peter. On the command of the DDCs, they control the flow rates in pipelines with particularly fine steps.
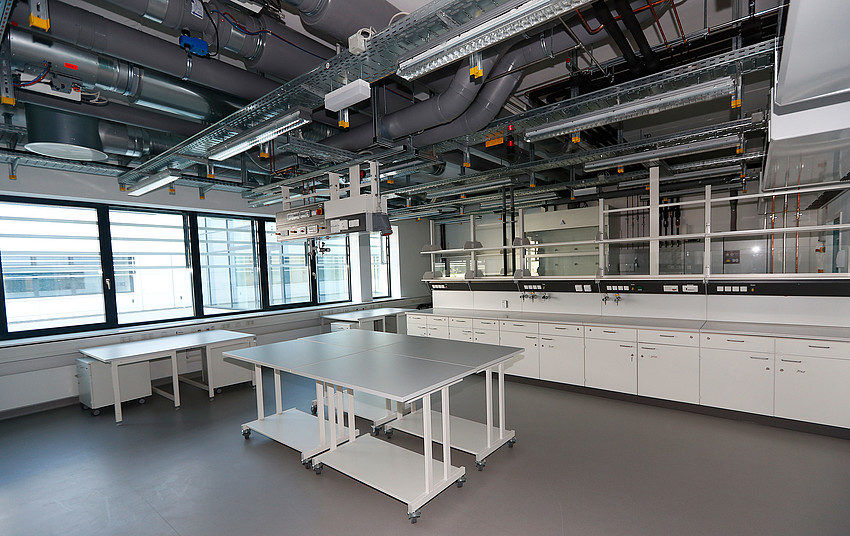
Suitable climate, individual for each zone
The high-precision control automation ensures that the required atmospheric conditions are maintained fully automatically around the clock in the laboratories and workshops. The “Made in Germany” software and hardware system from Kieback&Peter ensures that the temperature or humidity values are always reliably within the specified range at the specified location—even in connected laboratory cabinets. The plant also ensures that scientists can work with their sensitive equipment, including electron microscopes, with precision, or have breathing air free of welding smoke in the welding laboratories.
The team has solved the control of the boiler and combined heat and power plant using Modbus as the communication protocol. The air volume controllers of the laboratories and workshops communicate with the DDCs via BACnet. The team has also found an individual and user-friendly solution for the university’s internal ice storage and heat pump research project: The scientists can evaluate or assign all data and control commands of interest securely via their office PCs. In this way, it is not only the researchers who can benefit from smart building automation—the University of Bayreuth’s accounting office also has cause to celebrate: The Kieback&Peter system ensures that all energy-intensive plants are highly efficient and consume only as much primary energy as they actually need to.